LGI Supply Chain (MMS) allows for greater control over the healthcare supply chain, including contracts, distribution and logistics. Automate part of your procure-to-pay and plan-to-inventory process to better manage costs and optimize your resources.
of transactions processed electronically, without human intervention
less handling time completing page 415-00*
of purchase orders transmitted through the EDI module
*Results observed at a CISSS in Quebec following a change in process initiated by the Fixed Asset Management and Project Management modules.
Benefits
-
Gain greater visibility into the overall procurement process, budget allocation and accessing essential materials for healthcare delivery
-
Optimize logistics, merchandise storage and efficiency of care by reducing the risk of errors associated with order indexing
-
Improve patient safety by maintaining adequate stock levels with real-time data flow
-
Meet the unique needs of your healthcare facility with highly customizable settings
-
Improve staff efficiency by removing almost all repetitive manual tasks related to invoice processing
-
Benefit from integration with the Global Data Synchronization Network (GDSN) to access complete, up-to-date product information at all times
-
Quickly assess the efficiency of supply chain processes with a real-time snapshot of your budget, expenses, pending orders and inventory issues
-
Replace paper documentation with electronic versions and optimized workflows
-
Fine tune expense accounts by integrating them with your facility’s purchasing information and chart of accounts
Features
-
Customized contract and order management for multi-facility and multi-site operations
-
Automated stock replenishment based on security settings
-
Complete computerization of the requisition process with customizable templates
-
Consolidation of inventory products and direct purchases on the same order
-
Orders of non-catalogue products and splitting of quantities ordered on different dates
-
Centralization of tender processing, usage proposals and requests for quotations with suppliers
-
Detailed reporting with predictive risk analysis on inventory shortages
-
Integration with Axelos and Copilote warehouse management systems (WMS)
-
Compliance with Global Trade Identification Number (GTIN), Global Location Number (GLN) and United Nations Standard Products and Services Code (UNSPSC) standards
-
Dashboards, purchasing process reports and follow-up alerts for inventory and procurement planning
/lgi-supply-chain-inventory-module-1.jpg?width=800&height=800&name=lgi-supply-chain-inventory-module-1.jpg)
/lgi-supply-chain-doctor-smiling-module-2.jpg?width=800&height=800&name=lgi-supply-chain-doctor-smiling-module-2.jpg)
/lgi-supply-chain-male-smiling-module-3.jpg?width=800&height=800&name=lgi-supply-chain-male-smiling-module-3.jpg)
Discover our Modules
LGI Supply Chain is a suite of complementary modules designed to optimize healthcare facility supply chains. Facilities can deploy these modules as needed for greater efficiency in contracts, distribution, logistics, purchasing, inventory planning, and more.
Procurement, Purchasing, and Inventory
Automates a portion of purchasing, replenishment, and inventory management based on a processing calendar defined by system administrators. The module offers several interfaces connected to specialized systems, including operating room managers, pharmacy managers, and RFID technologies.
Electronic Document Interchange (EDI)
Integrates into the Procurement, Purchasing and Inventory Management module to help implement e-commerce solutions. Manages transactions including catalogues and contracts (832), orders (850), order acknowledgments (855), delivery notices (856) and invoices (810). The module improves the reliability and fluidity of data exchanged with suppliers.
Calls for Tenders, Usage Proposals, and Requests for Quotations
Supports procurement staff through various phases of the supplier negotiation process. The module integrates with the Electronic Requisition Management module, automatically generating bids, contracts and orders. It can synchronize with corporations and purchasing groups.
Electronic Document Management – Financial and Material Management
This model enables partial automation of invoice processing (in PDF or paper format) via character recognition scanning. Captured data is automatically entered in accounts payable and added to inventory. Authorization processes are then updated in real time, making it easier to manage the budget, commitments and financial implementation of projects.
Fixed Asset and Project Management
Automatically updates the fixed assets register by integrating with the General Ledger, Accounts Payable and Accounts Receivable modules of the LGI Financial solution. Simplifies depreciation calculations and ensures operational traceability by linking with the original transactions. Centralized register management provides users with a history of all transactions from every department in the facility.
Automated Transaction Accounting and Financial Statistics
Records real-time transactions resulting from procurement activities, product receipts and deliveries, as well as accounts payable operations. Interoperability with the Financial Management System ensures sound management of accounting entries and financial commitments.
Electronic Requisition Management
Speeds up the processing of requests by eliminating paper from the work flow. Requests are sent electronically to the Supply and Logistics team using barcodes or RFID technology. The module provides up-to-date information on inventory products, quantities, pending orders, inventory issues, suppliers and budget tracking. Each requisition is documented and automatically entered in the budget.
Integrated Resource Management (IRM) and Analytical Dashboards
This module simplifies and centralizes management of the fixed asset register, including new item creation, work-in-progress monitoring and depreciation and disposal calculations. It also facilitates financial reporting and can drill down to source transactions.
Inventory Products Distribution Centre and Purchase Order Cross-Docking
Integrates features to manage and centralize (partial or total) inventory products in an external warehouse. Products are identified at the distribution centre, then ordered as direct purchases from the centre’s affiliated supplier before being delivered to the facility.
Requisiton Receipt Web (New)
A web-based version of the Requisition Management module that provides access to dashboards and graphs illustrating product consumption. The new module simplifies the ordering and receiving of OptiLab products, with user-friendly browsing to facilitate searching for information on models, requisitions, products, and more.
FAQ on the technological upgrade
What does the technological upgrade involve?
This is a two-phase upgrade that merges and optimizes the LGI Financial (FMS) and LGI Supply Chain (MMS) databases. This upgrade provides access to next-generation web products and many immediate enhancements. Ultimately, the goal is to help care teams and administrative staff better serve patients.
What are the benefits of upgrading LGI Financial and LGI Supply Chain?
A technology upgrade improves the speed and overall performance of the product, primarily by merging the databases.
The operation also implements the technology architecture required to move to a web management mode. This new architecture lets you use the Budget and Requisition Receipt modules in web mode, as well as any other web module to be developed in the future. Software updates can be done remotely instead of manually at each workstation. Lastly, the upgrade includes 180 improvements to the interface and features based on client feedback.
Simplified telework
The solution is accessible remotely and updates are easier to deploy to the client environment
Increased speed and performance
Merging the databases boosts system performance and speed
Access to future web modules
The new technology gives access to the Budget Web modules and other future web modules
Enhanced user experience
Users can benefit from more than 180 interface enhancements and new features
What are the steps of the technological upgrade?
- Project planning
- Identification of key players
- Implementation of schedule
- Preparatory work
- Technical audit of the environment
- Database adjustment for tests if required
- Validation of technical prerequisites
- Testing period
- Installation of test environment
- Management of validation tests
- Production release planning
- Production launch
- Work in production
- Start of production operations
- Stabilization of environment
- Final adjustments
- Post-mortem and retrospective
- Project operationalization
How long does the upgrade take?
The time required to complete the FMMS technology upgrade depends on several factors, including database complexity and resource availability. Take, for example, a hospital with some 5,000 employees that issues nearly 40,000 purchase orders each year: the upgrade was completed in three months.
While our teams are used to planning for this type of project, their capacity is demand-driven, so we suggest that you contact us for an idea of a potential timeline.
ADDITIONAL RESOURCES
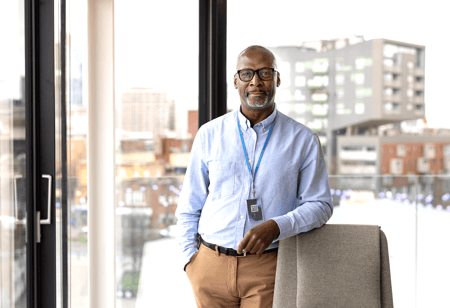
Modernizing Its Financial and Material Solutions: A Client Interview
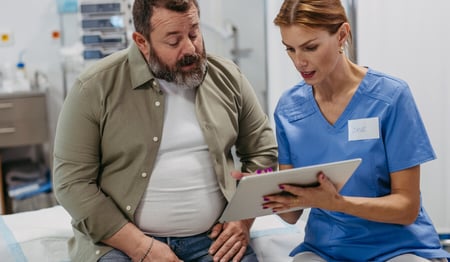
7 Ways Hospitals Improve Patient Experience with LGI
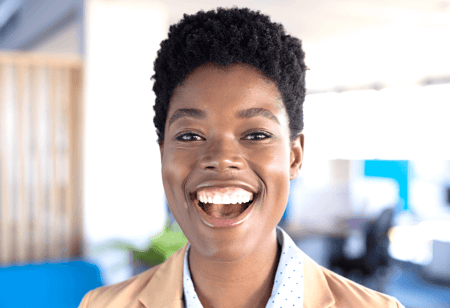
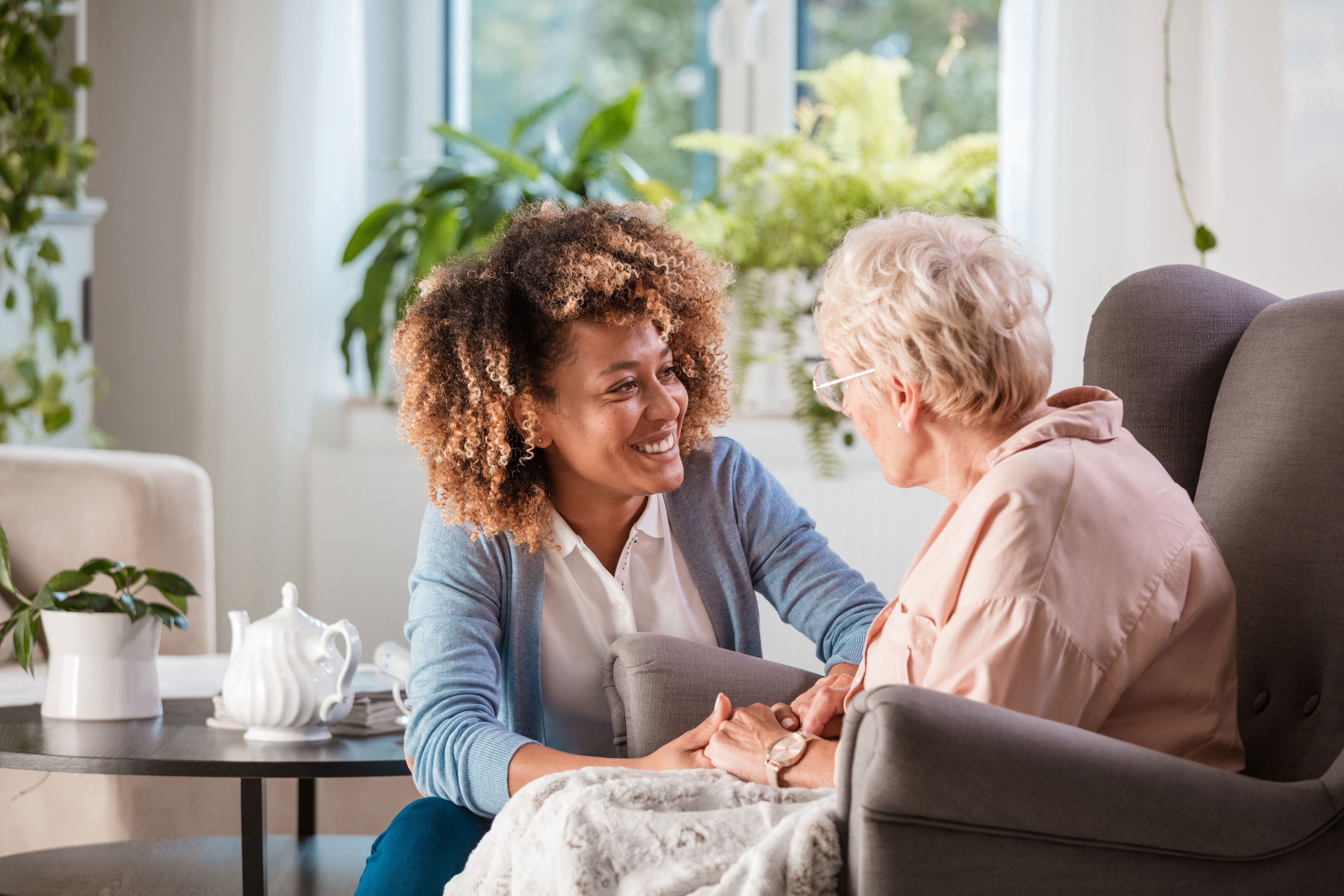
CASE STUDY
TRANSFORMING WORKFORCE MANAGEMENT AT THE FRED DOUGLAS SOCIETY
Discover how LGI Workforce Pro is helping FDS overcome challenges like outdated systems, inefficient reporting, and compliance complexities by integrating HR, payroll, and scheduling tools in a single platform.